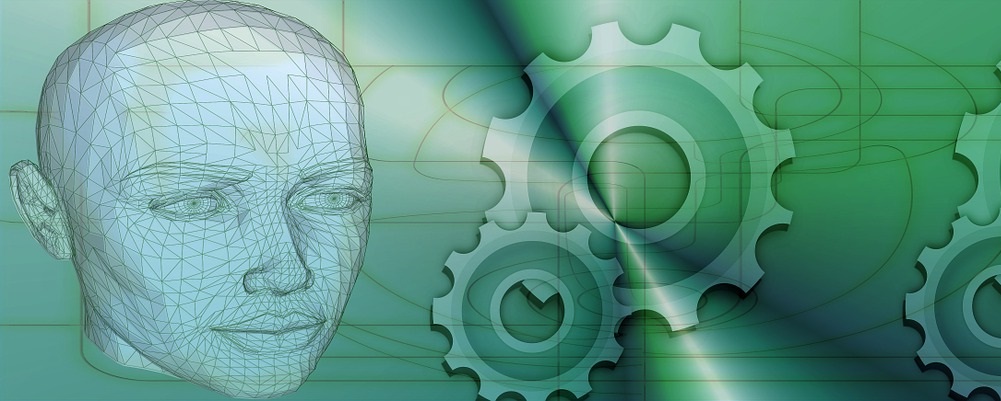
A recent Gartner study revealed that 83 percent of businesses are struggling to make meaningful progress on digital transformation. These findings are in stark contrast to another study of senior level IT professionals at manufacturing organizations regarding their satisfaction with Industrial Internet of Things, or IIoT, which connects machines and devices in industries such as transportation, power generation, and in this case, manufacturing. Eighty-six percent said they believe their solutions are very or extremely effective. These findings are particularly interesting since the majority of these manufacturing businesses are still in the earliest stages of IIoT adoption.
According to Bsquare’s IoT Maturity Index, there are five stages commonly associated with IIoT technology adoption. Each phase typically builds on the previous one allowing organizations to drive maximum value as they progress through the index. The stages include: 1) Device Connectivity, 2) Data Monitoring, 3) Data Analytics, 4) Automation and 5) Edge Computing.
Most manufacturing organizations have yet to progress beyond stage 3 to more mature tasks in IIoT, such as automation, which is where significant ROI can be unlocked. This lack of maturity is not due to a lack of effort. As a matter of fact, there are several barriers impacting an organization’s ability to move beyond the initial (and basic) stages of an IIoT deployment.
To understand where manufacturers are headed with their IIoT solutions, it’s important to understand where they are today, what challenges they’re facing, and how they can prepare to break through perceived limitations to benefit from more advanced capabilities.
Where are businesses at today?
Currently, most manufacturers have reached stages 1 and 2 of IoT maturity, device connectivity (67 percent) and data monitoring (62 percent). These businesses have become adept at collecting data from sensors and connected equipment and transmitting it to cloud databases for analysis. Many of these same businesses also are accustomed to leveraging dashboard and visualization tools to gain awareness of equipment status and orchestrate simple alerting.
However, less (47 percent) have reached Stage 3, data analytics, which is where many will find significant returns. Here, businesses are empowered to leverage machine learning, cluster analysis and artificial intelligence (AI) to identify data correlations in real-time. This step is essentially where the groundwork is laid for Stage 4: Automation. It’s at this stage that dynamic rules-based logic can be leveraged to orchestrate complex actions across an organization, including service ticketing and inventory adjustment requests.
Over time, applying machine learning and sophisticated analytics also enhances an IIoT system’s intelligence. As the system detects anomalous conditions on a production line, it increases data collection and transmission. Then it can execute a series of automated steps to correct the error, or automatically adjust operating parameters to minimize damage while also notifying a technician of the issue and repair urgency.
Why have so few companies reached automation?
Manufacturing plants produce massive amounts of data from multiple sources that may overwhelm existing IIoT systems. While the insights are right there waiting to be culled from the raw data streaming from factory systems and equipment, it’s buried within a massive labyrinth of complex datasets.
This data challenge can quickly be compounded by a human one. Lacking internal champions for an automation initiative or the right resources to extract relevant data can bring factory automation and digital transformation to a standstill.
How can manufacturers break through?
In order to enhance the potential for automation, manufacturers should take a practical approach to help minimize organizational and individual resistance, as well as build the foundation for more advanced capabilities, including:
Establishing common ground.
Although technology itself is a crucial element, a successful IIoT initiative is a cross- organizational effort built upon business goals shared among many stakeholders. Creating a culture receptive to reaching an end goal, such as automation, from the start will help keep parties engaged and focused on the ultimate reward.
Picking a business problem and objective.
Setting a clear definition for what your IIoT project is intended to solve is essential. For example, a clear, specific goal might be to automate calibration settings based on current environmental conditions to improve quality by 10%. An aimless initiative without a set methodology for measuring value will only waste time and resources.
Identifying current diagnostic IP and subject matter experts.
People with the training and knowledge to not only identify and diagnose problems, but also prescribe a solution, are critical. This can include engineers, mechanics and maintenance teams. Getting the right people involved at the right time, in the right capacity can accelerate almost any IIoT exercise by operationalizing what your team already knows.
Getting help when it’s needed.
If your business is struggling to reach the automation level due to technology or resource challenges, outsourcing is an advisable option. Having a data science team at your disposal can significantly increase your deployment’s quality of outcomes and time to value. These teams oftentimes have experience with like deployments helping your business steer clear of common hurdles.
Whatever the goal, IIoT systems have become a manufacturer’s secret weapon for leveraging their full repository of data now and into the future. By taking these steps before diving into an IIoT deployment, manufacturers will be on the path to leveraging automation to increase output, manage costs and improve productivity. But the level of sophistication doesn’t end there. Stage 5, edge computing brings distribution of analytics and orchestration to the device level for even greater computing power and quicker response to real-time conditions.
Edited by
Ken Briodagh